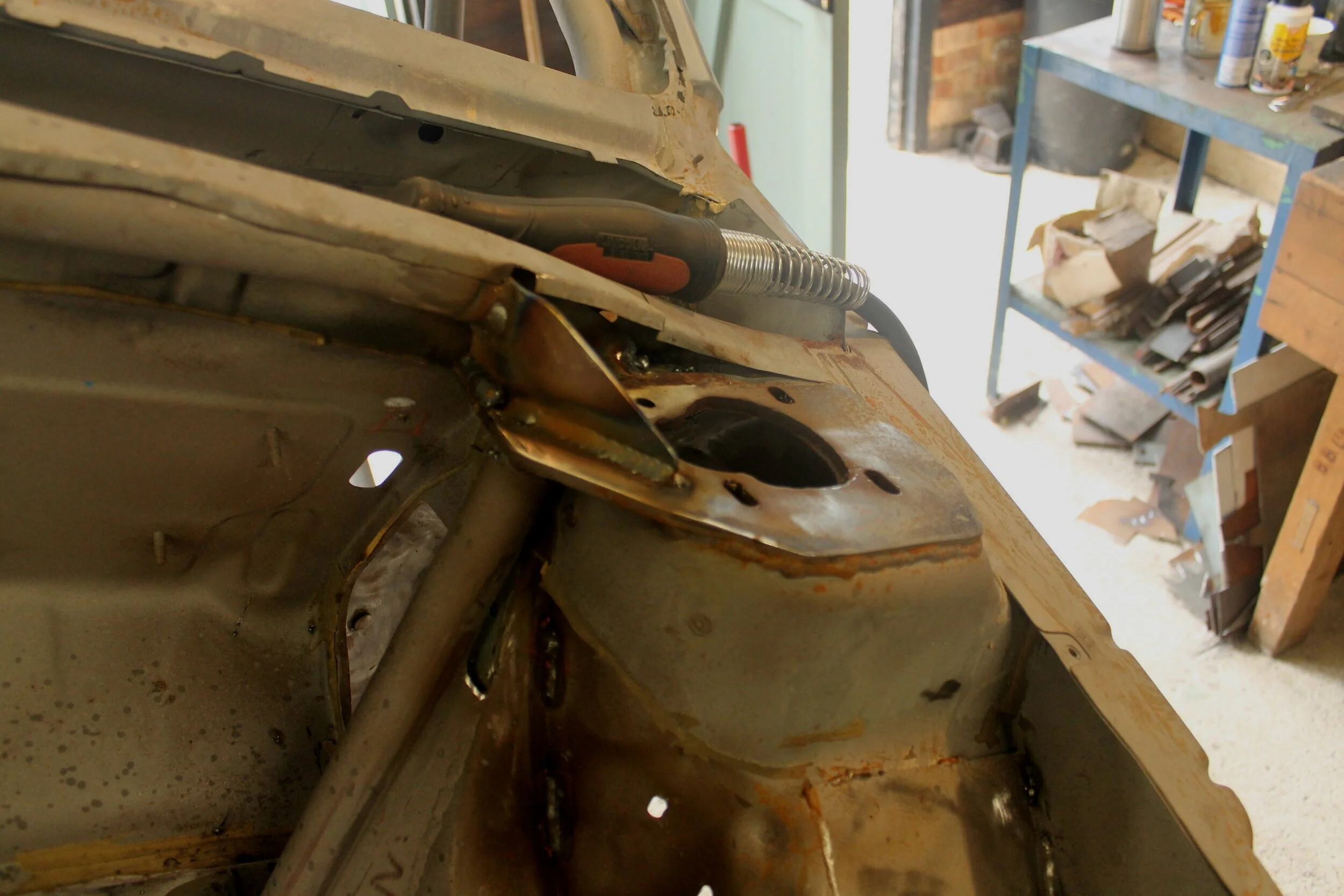
Fighting fit
“Tact time and throughput concerns of OEM factories are probably further down the priority list here than cleaning a bungalow’s first floor windows“
Attacking gravel roads presents quite a challenge for little thin shelled shopping vehicles. The relentless changing terrain requires confidence from the crew to navigate safely at speed, this confidence comes from a predictable chassis. To ensure every chassis movement is predictable, the car needs to have as close to no compliance. We should also mention at this point that because the car will have a novice crew on board, a predictable chassis is central to the ethos of this build, ensuring the TenSix won’t raise the white flag in competition (famously like it’s compatriots) being a close second. So much like a boxer the TenSix needs to be able to roll with the punches.
Motorsport UK rules state you may not modify any suspension mounting points for stage rally cars, so a fundamental re-design of the suspension system was out of the question. Motorsport UK do however allow “strengthening of factory suspension mounting points using the same material as the manufacturers unibody construction (body shell for those colloquial types) attached by welding”. Enter stage left the MIG welder (we wish it was TIG but the talent budget ran out on this project). Rear beam mounts, strut tops and wishbone mounts were all given the ‘doubler plate treatment’.
Doubler plates are pieces of sheet metal formed to match the contours of the body mounting in question, often thicker than the sheet metal used originally and welded in place around the edges. Doubler plates provide paths for stress to flow away from the original mounting to larger parts of the body shell that can absorb the stress without deforming. Less deformation means reduced suspension compliance… To add to Project TenSix’s doubler plates, the front struts were braced vertically to the precarious front wishbone mounts (due to a lack of subframe) in order to triangulate the front suspension loads. Joining up these two front ‘triangles’ is a strut brace, neatly hidden under the bonnet seal lip with a couple of subtle bends. The rear wishbone mounts had some extra threaded bosses welded in to spread the stress to a doubler plate inside the car, meaning the studded factory wishbones no longer fit… watch this space.
While spot welds are a rapid method of joining the large pressed panels that make up our beloved thin shelled shopping vehicles. The tact time and throughput concerns of OEM factories are further down the priority list here than cleaning a bungalow’s first floor windows. Seam welding is an age old motorsport shell preparation technique, whereby the spot weld seams (return bends pressed in place specifically for clamping with a spot welding torch) are joined by intermittent lengths of MIG weld beads. Welding intermittently reduces heat transferred into the panel and mitigates the risk of warping. These seam welds prevent each panel from moving against its adjoining panel. Across the car, this means that un-intended wheel geometry changes can be reduced, ensuring chassis predictability. Doubler plates and seam welds will be joined on stage in the next act by some scaffolding...


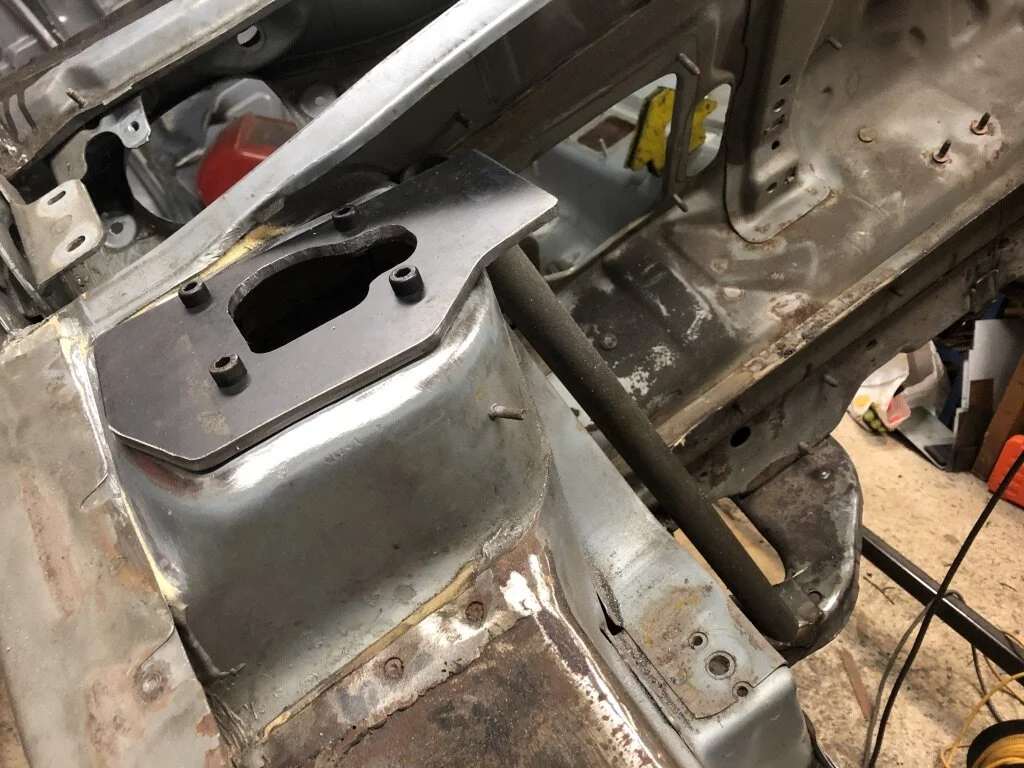

